♦This article is a refresh from one that Grant published on the Canadian Contractor, March 27, 2019.
There’s often confusion within the building industry between the terms vapour barrier (VB)and vapour retarder (VR). Let’s help clarify the differences. The term vapour barrier should be reserved to referencing a barrier that essentially does not allow water vapour to pass, and is designated as vapour impermeable. In contrast, a vapour retarder should be used to describe a barrier that has a level of vapour permeance(or vapour control). Understanding the difference between these terms is critical knowledge for building designers and contractors. Equally important is knowing the permeance of the given material.
A sneak peak at vapour retardant barriers
Dr. Joseph Lstiburek, are renowned building scientist and principal of Building Science Corporation, expanded on the Canadian General Standards Board(CSGB)approach by categorizing the water vapour permeance of vapour retarders inTable1below; where a perm is a unit of measurement usually reserved for water vapour permeance(1 US Perm = 0.66SI Perm = 57.2 ng/(s m2Pa)). Lstiburek designated that a vapour barrier is a Class I vapour retarder(Lstiburek, 2011)
Defining Term | Vapour Retardance Class (Lstiburek, 2011) | US Perm | Material Examples (Perm) (Building Science Corporation, 2015) |
Vapour impermeable (vapour barrier) | Class I Vapour Retarder | < 0.1 Perm | Polyethylene “poly” sheet – 6mil (0.06) |
Vapour semi-impermeable | Class II Vapour Retarder | 0.1 – 1.0 Perm | VR Primer, Oil-based paints, vinyl coverings |
Vapour semi-permeable | Class III Vapour Retarder | 1.0 – 10 Perm | Asphalt Felt -#15, OSB, plywood, latex-based paints |
Vapour permeable | 10 Perm | Typar® (9-15), Tyvek® (58) |
In order to control vapour diffusion (the movement of water vapour through a material), building codes require buildings to have a vapour barrier within the wall. The mandated vapour barrier is designated as a membrane that has perm rating less than 1.0 US perm (Note that this membrane would be classified as a Class II vapour semi-impermeable retarder or less, as defined by Table 1 above).
More often than not, this is satisfied by means of a polyethylene “poly” sheet, i.e. a plastic impermeable vapour barrier, within the wall. Notice the permeance of poly as shown in Table 1 (0.03 Perm) is well below the required US Perm of 1 required by code.
Installing the wrong barrier can result in building failure
In Canada and northern U.S. states, where heating dominates over cooling, the vapour retarder is installed on the warm side – typically directly behind the drywall. The location of the vapour retarder prevents the warm and relatively humid air to travel (diffuse) into the wall where it may condense (interstitial condensation).
Building scientists agree that the use of vapour impermeable barriers are rarely necessary and in fact can be a poor strategy in all except the coldest climates. This is because the use of vapour impermeable barriers have several significant drawbacks. First, the vapour impermeable barrier is on the wrong side during the summer months in air-conditioned buildings — and today most buildings are air conditioned. Second, the wall assembly is restricted to dry on the non-vapour barrier side. And third, construction itself is not perfect, and neither is the installation of a vapour barrier. While these barriers need* be continuous, in reality there are always going to be some unintentional holes through the vapour barrier. This could occur perhaps at joints, but more typically it’s where trades such as electricians have punched a hole through the barrier and was covered up before it was noticed and repaired. The problem is that this results in a concentration of humid air flowing through that hole, while the envelope is limited to dry to only the exterior (if a vapour barrier is installed on the inside). Buildings should be constructed to be robust so that when they do suffer a localized failure, they can recover. The fact is, at some point, somewhere, a building element will fail — something as simple as deteriorated sealant at a window.
*Although vapour barriers are not critical to be continuous, it is critical for air barriers to be continuous. Typically, in residential construction the poly vapour barrier doubles as the air barrier, therefore requiring the poly sheet to be continuous.
The solution
It’s quite simple — don’t use vapour impermeable barriers (under standard constructions), i.e. vapour retarders with a U.S. perm rating less than 0.1 perm. Instead, use the most permeable vapour retarder that works with the building envelope assembly. Typically vapour impermeable barriers can be avoided completely in all building types except those with very high humidity levels, such as indoor pools and hospitals, and sometimes those in extreme cold regions.
Some things to note. It is important that the vapour permeance of building materials within the assembly are installed so that the lowest permeability rating material is installed on the warm side, gradually increasing as you move through the building assembly. If a vapour impermeable barrier is required, then only install one – this is critical. This includes low vapour permeable building materials like foil faced rigid insulation. Do not create a vapour sandwich with these low permeance membranes and materials by placing them on the outside of a building with poly on the inside. If you do, you significantly impact the buildings durability redundancy by reduce drying when, not if, your assembly is breached with liquid water or water vapour.
A myth exposed: poly is not required by code
So why do vapour impermeable barriers, such as poly, continue to be installed, almost as if they are the construction standard? Part 9.25.4.2 of the National Building Code of Canada (NBCC) states “vapour barriers shall have a permeance not greater than 60 ng/(Pa s m2)…”. This equates to approximately ~1 US Perm**. In the subsequent NBCC part, polyethelyne is directly referenced as a suitable vapour barrier. However, its vapour permeance is 0.06 perm – an order of magnitude more vapour impermeable than what’s required by code. Additionally, it is also written that any other material other than polyethylene shall conform to “Vapour Barrier, Sheet, Excluding Polyethylene, for Use in Building Construction.” This could suggest to the reader that poly is the gold standard, when realistically it should be left exclusively for specific conditions where high vapour diffusion is a design concern. This may also help explain the confusion of vapour barriers and retarders, and why greater vapour impermeability is not (usually) better.
** Note that the NBCC refers to a barrier with less than 1 US perm as a “vapour barrier”. However, based on Lstiburek’s Table, the reference to “vapour barriers” should be exclusively reserved when referring to “vapour impermeable barriers” (ie. those with less than 0.1 perm).
Alternatives to satisfy code
Acceptable options that satisfy code, include vapour retardance paint with an air sealed drywall approach (however, this approach may not be approved by the authority having jurisdiction as an air barrier; in which case one will have to be provided), or a vapour variable retarder – typically referred to as a “smart” vapour retarder. The permeability of smart vapour retarders change with humidity — typically from less than 1 perm when the cavity is dry, to greater than 10 perms when the cavity has high relative humidity. These membranes promotes drying within the wall when it becomes wet. These are good alternative options, especially for buildings with exterior insulation (remember vapour sandwiches?). For additional vapour retarder options and a list of vapour permeability of commonly used materials, refer to the data formulated by Building Science Corporation – Info-500: Building Materials Property Table.
It is important however that the final selection of a vapour retarder as well as the placement of materials within a building assembly be completed by a building professional with a good understanding of building sciences. A “I’ve built it this way for 30 years” contractor may not be sufficient proof of their building science constructions.
Which climate zones, and which requirements?
In his categorization of water vapour permeance of various retarders, Dr. Joseph Lstiburek continued his analysis with recommendations concerning which climate zones require a vapour retarder, and what type it should be. His recommendations, based on a combination of field experience, laboratory testing, and hygrothermal modeling using WUFI, are presented below in Table 2 (Lstiburek, 2011). Lstiburek’s research pointed out: “In Chicago [Climate Zone 5] where plywood or OSB sheathing is used, an unfaced fiberglass batt can be installed within the wall cavity and gypsum board painted with latex paint (Class III vapor retarder) is required on the interior of this assembly. If this assembly is moved to Minneapolis [climate zone 7], a Class II vapor retarder is required on the interior (a kraft paper faced fiberglass batt).” As shown by Lstiburek in Table 2, there is no requirement for a Class I vapour retarder (vapour impermeable barrier). However, a vapour impermeable barrier may be required in climate zone 8 or, as previously discussed, in other special circumstances such as a humid swimming pool room.
Wall Assembly: Climate Zone |
Exterior Sheathing Greater than 1.0 perm |
Exterior Sheathing Less than or equal to 1.0 perm, greater than 0.1 perm |
Assembly Less than or equal to 0.1 perm |
1 | Not required | Not required | Not required |
2 | Not required | Not required | Not required |
3 | Not required | Not required | Not required |
4 (not marine) | Class III | Class III | Class III |
4 (marine) | Class III | Class II | Class III* |
5 | Class III | Class II | Class II* |
6 | Class II | Class II | Class II* |
7 | Class II | Class II | Class II* |
8 | Not analysed | Not analysed | Not analysed |
*Additionally, the interior surface of the exterior sheathing shall be maintained above the dew point temperature of the interior air.
For reference, each climate zone to which Lstiburek referred is defined in Figure 1, can be cross-referenced on a map of Canada in Figure 2 from the U.S. map in Figure 3. Zones 3 and 4 are divided into A, B, and C representing moist, dry, and marine climates respectively. It can be noted that cooling is the only important factor for zones 1 and 2, heating and cooling for zones 3 and 4, and heating only for zones 5, 6, 7, and 8.
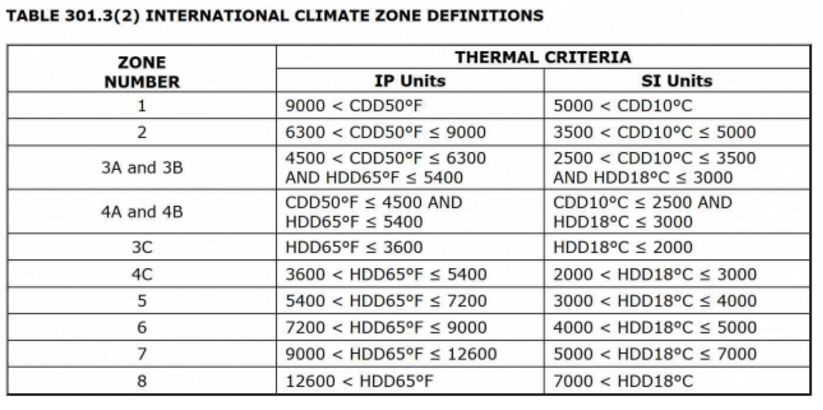
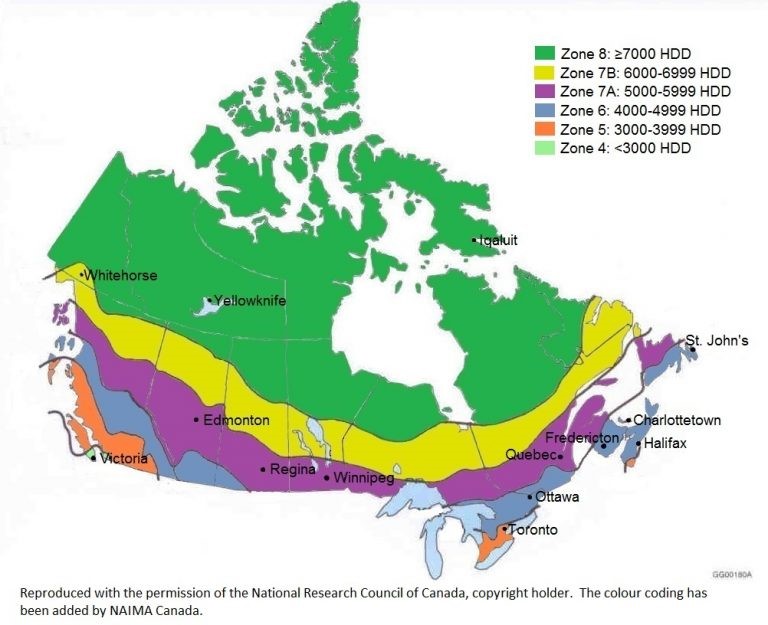
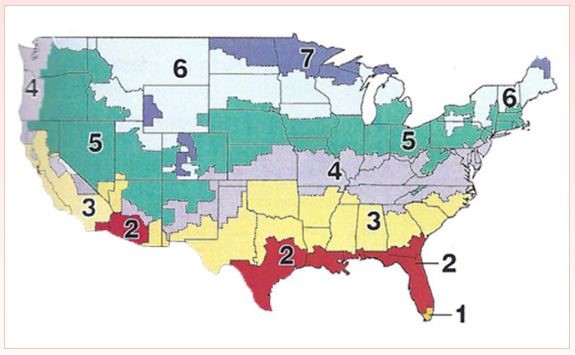
An industry resistant to change
In summary, it is critical to understand vapour retarders — their permeability, function, and where in the building assembly they are needed. Under normal conditions there is no requirement for a polyethylene vapour impermeable barrier (Class I vapour retarder). In fact, their use as a vapour retarder can be dangerous and should be avoided due to their suffocating drying potential. Their requirement came from limited research and understandings many decades ago*** but has had a significant and ever-lasting impact on the building industry.
Many building contractors, and even some building professionals, will still say that there must be a poly vapour barrier. This is an excellent example of how resistant the construction industry can be to change. Building scientists have known for years that there are in fact much better options to building a well-designed building, while satisfying the building code’s call for a Class II vapour retarder (“vapour barrier”), other than a poly sheet. Simply put, understanding vapour flow and building physics is critical for long term building durability.
***Bill Rose dives deep into the history polyethylene sheets in his “Water in Buildings” book.
References
- Building Science Corporation. (2015, April 24). Info-500: Building Materials Property Table. Retrieved from Building Science Corporation
- Lstiburek, J. (2011, April 15). BSD-106: Understanding Vapour Barriers. Retrieved from Building Science Corporation